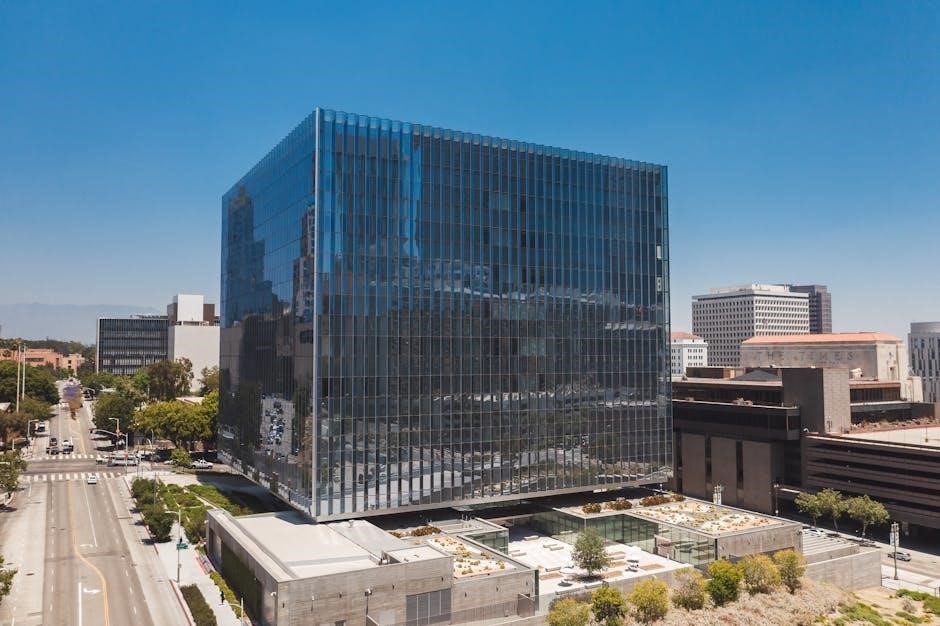
The Regulation on Workplace Health and Safety (Règlement sur la santé et la sécurité du travail) ensures a safe work environment by outlining employer and employee responsibilities, regular updates, and enforcement mechanisms to promote health and safety standards.
1.1 Overview of the Regulation
The Regulation on Workplace Health and Safety (Règlement sur la santé et la sécurité du travail) establishes the framework for ensuring the well-being of workers in various industries. It outlines definitions, scope, and general provisions to guide employers and employees in maintaining a safe work environment. The regulation applies broadly, covering physical environments, equipment safety, and personal protective equipment (PPE) requirements. It emphasizes hazard identification, risk prevention, and compliance measures to protect workers’ health and safety. Regular updates ensure alignment with evolving workplace risks and technologies, making it a cornerstone of occupational safety in Canada.
1.2 Historical Background and Development
The Regulation on Workplace Health and Safety has evolved significantly since its inception. Originally established in 1986 under the Canada Labour Code, it was designed to address growing concerns about workplace accidents and illnesses. Over the years, amendments such as those in 2001 and 2023 have expanded its scope to include updated safety standards, hazard prevention measures, and stricter enforcement mechanisms. The regulation draws from international best practices and adapts to technological advancements, ensuring it remains relevant in safeguarding workers’ health and safety across various industries. This continuous development reflects a commitment to creating a safer and healthier work environment for all employees.
1.3 Key Amendments and Updates
Recent updates to the Regulation on Workplace Health and Safety include the 2023 amendments, which strengthened employer obligations and enhanced worker protections. These changes introduced stricter requirements for hazard assessments, improved incident reporting protocols, and expanded training programs for high-risk tasks. Additionally, the regulation now incorporates provisions for mental health and ergonomic standards, reflecting a broader understanding of workplace safety. Enforcement mechanisms were also bolstered, with increased penalties for non-compliance. These updates align with global trends in occupational health and safety, ensuring the regulation remains effective in addressing contemporary workplace challenges and fostering a culture of prevention and accountability.
Legal Framework Governing Workplace Health and Safety
The Canada Labour Code and provincial regulations establish the legal foundation for workplace health and safety, ensuring compliance with national and regional standards to protect workers effectively.
2.1 The Canada Labour Code and Its Relevance
The Canada Labour Code is a cornerstone of workplace health and safety legislation, governing federal jurisdictions and ensuring employers provide a safe work environment. It outlines specific responsibilities for both employers and employees, emphasizing hazard prevention and incident reporting. The Code also establishes enforcement mechanisms, including inspections and penalties for non-compliance. It plays a crucial role in harmonizing workplace safety standards across Canada, particularly in industries under federal oversight. Regular updates to the Code reflect evolving workplace risks and technologies, ensuring it remains relevant and effective in safeguarding workers’ health and safety.
2.2 Provincial and Territorial Regulations
Provincial and territorial regulations complement the Canada Labour Code by addressing workplace health and safety at the regional level. Each province and territory has its own legislation, such as Ontario’s Occupational Health and Safety Act, which outlines specific obligations for employers and workers. These regulations often include industry-specific requirements, such as construction or healthcare, to address unique risks. Provincial laws also establish enforcement mechanisms, including inspections and penalties, to ensure compliance. Employers are typically required to conduct risk assessments, implement safety measures, and provide training. These regulations are regularly updated to reflect changing workplace conditions and align with national health and safety standards.
2.3 Specific Provisions for Federal and Provincial Jurisdictions
Federal and provincial jurisdictions have distinct regulations tailored to their respective governance. The Canada Labour Code applies to federal workplaces, while provinces enforce their own laws, such as Ontario’s Occupational Health and Safety Act. Specific provisions address hazards unique to federal sectors, like maritime or transportation. Provincial laws often include detailed requirements for industries such as construction or healthcare. Federal regulations emphasize hazard identification and control, while provinces may focus on enforcement through inspections and penalties. Both levels require employers to provide safe environments, conduct risk assessments, and train workers. These provisions ensure compliance with national standards while adapting to regional workplace conditions and industry-specific risks.
Roles and Responsibilities in Workplace Health and Safety
Employers must ensure hazard control and provide training, while employees must follow safety protocols. Safety officers conduct inspections, audits, and enforce compliance to maintain a safe work environment.
3.1 Employer Obligations
Employers are legally required to ensure a safe work environment by identifying and controlling hazards, providing necessary training, and maintaining equipment. They must conduct regular risk assessments, implement safety measures, and ensure compliance with regulations. Employers are also responsible for reporting incidents, providing personal protective equipment (PPE), and establishing emergency response plans. They must consult with employees and safety committees to address concerns and continuously improve workplace safety standards.
3.2 Employee Responsibilities
Employees must adhere to workplace safety rules, use provided personal protective equipment (PPE), and report hazards or incidents to their employer. They are expected to follow safe work practices, participate in training sessions, and cooperate with safety measures implemented by their employer. Employees should also actively identify and report potential risks, contributing to a safer work environment. Additionally, they must comply with emergency procedures and respect health and safety instructions provided by their employer or safety officers. By fulfilling these responsibilities, employees play a crucial role in maintaining workplace safety and protecting their own well-being and that of their colleagues.
3.3 Role of Safety Officers and Committees
Safety officers and committees are integral to workplace health and safety management. They conduct regular inspections to identify hazards and ensure compliance with safety regulations. Safety officers provide guidance on safe practices, investigate incidents, and recommend preventive measures. Committees, comprising representatives from both management and employees, foster collaboration to address safety concerns. They facilitate communication, monitor incident trends, and implement corrective actions. Their collective efforts ensure a proactive approach to workplace safety, fostering a culture of prevention and continuous improvement. By addressing risks and promoting awareness, they contribute significantly to safeguarding employees’ well-being and maintaining a safe work environment.
Risk Assessment and Prevention Strategies
Risk assessment involves identifying workplace hazards, evaluating risks, and implementing preventive measures to ensure compliance with safety standards and protect employees from potential harm effectively.
4.1 Hazard Identification and Evaluation
Hazard identification and evaluation are critical steps in ensuring workplace safety. Employers must systematically identify potential hazards, assess associated risks, and implement controls to mitigate them. This process involves evaluating physical, chemical, and biological risks, as well as ergonomic and psychosocial factors. Regular inspections, employee feedback, and incident analysis are essential tools for identifying hazards. Once identified, risks are evaluated based on their likelihood and potential impact. Employers must then prioritize mitigation measures, such as eliminating hazards, substituting unsafe equipment, or using personal protective equipment. Continuous monitoring ensures the effectiveness of these controls, safeguarding workers and complying with regulatory requirements. This systematic approach is vital for preventing accidents and promoting a safe work environment.
4.2 Risk Control Measures
Risk control measures are essential for minimizing workplace hazards. Employers must implement a hierarchy of controls, starting with elimination or substitution of hazards when possible. Engineering controls, such as ventilation systems or safety equipment, are next. Administrative controls, like safe work procedures and training, further reduce risks. Personal protective equipment (PPE) is used as a last resort. Regular monitoring ensures these measures remain effective. Employers must also adapt controls to evolving workplace conditions and employee needs. Clear communication and training on risk control measures are vital for ensuring compliance and fostering a safety-focused culture. These measures collectively protect workers and maintain a safe working environment, aligning with regulatory standards and best practices.
4.3 Emergency Preparedness and Response
Emergency preparedness and response are critical components of workplace health and safety. Employers must develop and implement comprehensive emergency plans tailored to potential risks, such as fires, spills, or natural disasters. These plans include evacuation procedures, first aid availability, and communication protocols. Regular drills and training ensure employees are prepared to respond effectively. Employers must also maintain emergency equipment, like fire extinguishers and first aid kits, and ensure their accessibility. Incident reporting and post-emergency reviews help identify areas for improvement. A well-prepared workplace minimizes risks, protects employees, and ensures compliance with regulatory standards, fostering a culture of safety and readiness. Proper emergency planning is essential for safeguarding lives and property.
Workplace Health and Safety Standards
The regulation establishes standards for workplace design, equipment safety, and personal protective equipment (PPE), ensuring a safe environment and minimizing risks to employee health and well-being.
5.1 Physical Environment and Workplace Design
The regulation emphasizes the importance of designing workplaces to prevent hazards and ensure a safe physical environment. Employers must assess and adapt workspaces to suit specific tasks, ensuring adequate lighting, ventilation, and emergency exits. The layout should minimize risks of accidents, such as tripping or falling, and provide ergonomic conditions to reduce physical strain. Regular inspections are required to maintain compliance with safety standards. Additionally, workplaces must be designed to accommodate employees with disabilities, promoting inclusivity and accessibility. By focusing on these elements, the regulation aims to create adaptable and secure environments that support employee health and productivity while adhering to legal requirements and best practices in workplace safety.
5.2 Equipment Safety and Maintenance
Employers are required to ensure all equipment is safe, properly maintained, and suitable for its intended use. Regular inspections and maintenance must be conducted to identify and address potential hazards. Equipment should be equipped with necessary safety features and guards to prevent injuries. Workers must be trained on the correct use, operation, and maintenance procedures. Records of maintenance and inspections must be kept to demonstrate compliance. Additionally, employers must ensure that equipment meets current safety standards and regulations. Proper equipment safety and maintenance practices are crucial to preventing workplace accidents and ensuring the well-being of employees while adhering to legal requirements and industry best practices.
5.3 Personal Protective Equipment (PPE) Requirements
Employers must provide and ensure the use of appropriate Personal Protective Equipment (PPE) to protect workers from hazards. PPE includes items like helmets, gloves, safety glasses, and respirators, selected based on the specific risks of each task. Workers must be trained on the proper use, maintenance, and storage of PPE; Employers are responsible for ensuring PPE is in good condition and replaced when necessary. Employees must wear PPE as required and follow all safety protocols. Compliance with PPE requirements is essential to minimize workplace injuries and illnesses, ensuring a safer working environment in accordance with health and safety regulations.
Training and Education in Workplace Safety
Employers are required to provide comprehensive training programs ensuring workers understand workplace hazards, safety protocols, and emergency procedures, promoting a culture of safety and compliance.
6.1 Employer Obligations for Training
Employers are legally required to provide comprehensive health and safety training to all employees, ensuring they understand workplace hazards, prevention methods, and emergency procedures. This training must be adapted to the specific risks associated with each task and work environment. Employers must also ensure that workers are informed about the safe use of equipment, proper handling of hazardous materials, and the importance of personal protective equipment (PPE). Additionally, employers are responsible for maintaining records of all training activities and ensuring that training is refreshed periodically to reflect new regulations or workplace changes. This obligation is a cornerstone of fostering a culture of safety and compliance.
6.2 Mandatory Training Programs for Workers
Mandatory training programs for workers are essential to ensure compliance with health and safety regulations. These programs cover fundamental topics such as hazard identification, emergency response procedures, and the proper use of personal protective equipment (PPE). Specifically, workers must receive training on workplace-specific risks, such as handling hazardous materials or operating machinery. Employers are required to provide these programs, which must be adapted to the nature of the work and the level of risk involved. Training must also include practical exercises and evaluations to confirm understanding. By ensuring all workers are adequately trained, employers can significantly reduce workplace accidents and promote a safer working environment. Regular updates to training programs are also mandated to reflect new regulations or emerging risks.
6.3 Specialized Training for High-Risk Tasks
Specialized training is required for workers performing high-risk tasks, such as handling asbestos, working at heights, or operating heavy machinery. These programs go beyond basic training, focusing on specific hazards and advanced safety protocols. Employers must ensure that workers receive comprehensive instruction tailored to their roles, including practical simulations and scenario-based training. For example, asbestos handling requires training on safe removal techniques and personal protective equipment (PPE) usage. Regular recertification is mandatory to maintain proficiency and adapt to new safety standards. By providing specialized training, employers can minimize risks associated with complex tasks and ensure compliance with health and safety regulations, protecting both workers and the organization from potential liabilities.
Enforcement and Compliance Mechanisms
The regulation ensures compliance through regular inspections, audits, and penalties for non-compliance. Employers must report incidents and maintain safety records to uphold accountability and legal standards effectively.
7.1 Inspections and Audits
Inspections and audits are critical components of enforcement under the Regulation on Workplace Health and Safety. Regulatory bodies, such as the CNESST, conduct regular inspections to ensure compliance with safety standards. These inspections may include evaluating workplace conditions, reviewing incident reports, and assessing risk management practices. Employers are required to cooperate fully, providing access to records and premises. Audits may also be triggered by incidents or complaints, ensuring that corrective actions are implemented. Internal audits by employers themselves are encouraged to monitor compliance proactively. Non-compliance can result in penalties, reinforcing the importance of adhering to safety regulations to protect workers and maintain a safe work environment.
7.2 Penalties for Non-Compliance
Non-compliance with the Regulation on Workplace Health and Safety can result in significant penalties, including fines and legal actions. Employers who fail to meet safety standards may face fines up to $100,000 for individuals and $500,000 for companies. Repeat offenses can lead to increased penalties. The CNESST, the regulatory authority, enforces these measures to ensure adherence to safety protocols. Penalties are imposed to deter violations and protect worker well-being. Employers must address non-compliance promptly to avoid legal consequences and maintain a safe workplace environment. These enforcement measures are essential for upholding the regulation’s objectives and safeguarding employee health and safety.
7.3 Reporting Incidents and Accidents
Under the Regulation on Workplace Health and Safety, employers must immediately report all work-related incidents and accidents to the relevant authorities. This includes accidents resulting in injury, occupational diseases, and dangerous occurrences. Employers are required to complete and submit specific forms detailing the incident, including the cause, affected individuals, and corrective actions taken. Failure to report incidents can lead to penalties. The CNESST oversees this process, ensuring compliance and follow-up investigations. Accurate and timely reporting is crucial for maintaining workplace safety, preventing future incidents, and supporting affected workers. Employers must also maintain records of all reported incidents for legal and regulatory purposes. This ensures accountability and continuous improvement in workplace health and safety standards.
Specialized Regulations for Specific Industries
Specific industries like maritime, construction, and healthcare require tailored safety regulations due to unique risks. These sectors have distinct protocols to ensure worker safety and compliance with health standards.
8.1 Maritime Workplaces
Maritime workplaces are subject to specific health and safety regulations due to unique risks such as exposure to hazardous substances, physical hazards, and confined spaces. Employers must conduct thorough risk assessments, provide specialized training, and ensure compliance with safety standards. Emergency preparedness, including evacuation plans and fire safety measures, is critical. Personal protective equipment (PPE) is mandatory, and regular inspections are required to maintain a safe working environment. These regulations aim to protect workers from occupational hazards and ensure adherence to both national and international maritime safety standards. Compliance is enforced through audits and inspections by relevant authorities.
8.2 Construction Industry
The construction industry is subject to specific health and safety regulations due to its high-risk nature. Employers must ensure hazard assessments are conducted, and safety measures are implemented to mitigate risks such as falls, equipment malfunctions, and structural collapses. Mandatory training programs for workers, including fall protection and heavy machinery operation, are essential. Personal protective equipment (PPE), such as hard hats and harnesses, must be provided and worn. Regular site inspections and compliance with safety standards are enforced to prevent accidents. These regulations aim to create a safer working environment and reduce occupational injuries in the construction sector. Adherence to these rules is critical for protecting workers and ensuring project safety.
8.3 Healthcare and Laboratory Settings
Healthcare and laboratory settings require specialized health and safety regulations to protect workers from biological, chemical, and physical hazards. Employers must implement infection control measures, proper handling of hazardous materials, and provide personal protective equipment (PPE) such as gloves and masks. Regular training on emergency procedures, including spill management and exposure protocols, is mandatory. Laboratories must adhere to strict safety standards for equipment operation and waste disposal. These regulations aim to minimize risks associated with pathogens, chemicals, and other potential hazards, ensuring a safe environment for healthcare professionals and laboratory staff. Compliance with these standards is crucial to prevent occupational illnesses and accidents in these high-risk settings.
International Perspectives on Workplace Health and Safety
Global standards, such as those from the EU and ILO, influence Canadian regulations, emphasizing collaboration to enhance workplace safety and health through shared best practices and compliance frameworks.
9.1 Comparison with European Regulations
The Canadian Regulation on Workplace Health and Safety draws parallels with European frameworks, emphasizing similar goals of preventing workplace risks and ensuring safe environments. Both systems require employers to conduct risk assessments and implement preventive measures. European regulations, such as the EU’s Framework Directive (1989), mirror Canada’s approach by mandating employer responsibilities and worker participation. However, Europe’s enforcement often involves stricter penalties and more detailed reporting requirements. Canada’s framework, while aligned with global standards, adapts to its federal and provincial structures, creating a centralized yet flexible system. Both regions prioritize continuous improvement in workplace safety, reflecting shared international commitments to worker well-being.
9.2 Global Standards and Best Practices
Global standards for workplace health and safety emphasize consistent practices to protect workers worldwide. The Regulation on Workplace Health and Safety aligns with international frameworks, such as those set by the International Labour Organization (ILO), which advocate for hazard identification, risk assessment, and preventive measures. The ILO’s conventions on occupational safety and health provide a foundation for policies like Canada’s Règlement sur la santé et la sécurité du travail. Best practices include regular training, proper use of personal protective equipment (PPE), and robust emergency response plans. These standards ensure a safer work environment and adapt to evolving industry needs, fostering a culture of continuous improvement in workplace safety globally.
9.3 Impact of International Agreements
International agreements significantly influence workplace health and safety regulations. The Règlement sur la santé et la sécurité du travail aligns with global accords, such as the ILO’s Occupational Safety and Health Convention, which sets universal standards. These agreements emphasize preventive measures, employee training, and hazard control. For instance, the ILO’s framework on workplace health promotion encourages countries to adopt comprehensive policies. Canada’s adherence to these agreements ensures harmonization of safety practices across borders, fostering a safer work environment. Such alignment not only enhances compliance but also promotes the sharing of best practices, ultimately benefiting workers and employers by creating a more consistent and protective regulatory landscape worldwide.
Emerging Trends in Workplace Health and Safety
Emerging trends include the integration of advanced technologies like AI and automation to enhance safety monitoring, as well as a growing focus on mental health and well-being.
10.1 Role of Technology and Automation
Technology and automation are revolutionizing workplace health and safety by enhancing monitoring, incident prevention, and data analysis. Advanced systems like AI and IoT enable real-time hazard detection, improving response times and reducing risks. Automation minimizes human exposure to dangerous tasks, while wearable devices track worker well-being. Digital platforms streamline compliance with regulations and facilitate training. These innovations not only optimize safety protocols but also foster a culture of proactive risk management, ensuring safer and more efficient work environments.
10.2 Impact of Artificial Intelligence
Artificial Intelligence (AI) significantly enhances workplace health and safety by enabling predictive analytics, real-time monitoring, and personalized safety recommendations. AI systems can analyze historical data to identify potential hazards, recommend preventive measures, and optimize safety protocols. Additionally, AI-powered tools facilitate incident reporting and investigation, ensuring compliance with regulations like the Règlement sur la santé et la sécurité du travail. By automating routine safety tasks, AI allows organizations to focus on proactive risk management, fostering a safer and more efficient work environment while reducing human error and enhancing overall safety standards.
10.3 Future Challenges and Opportunities
The future of workplace health and safety presents both challenges and opportunities. Advances in technology, such as AI and automation, offer enhanced monitoring and training tools, improving compliance with regulations like the Règlement sur la santé et la sécurité du travail. However, adapting to rapidly evolving technologies while ensuring ethical use remains a challenge. Mental health and psychological safety are gaining prominence, requiring updated policies. Additionally, climate change and sustainability concerns are integrating into safety standards, creating new opportunities for innovation. Balancing these advancements with practical implementation will be key to fostering a safer, more resilient work environment.