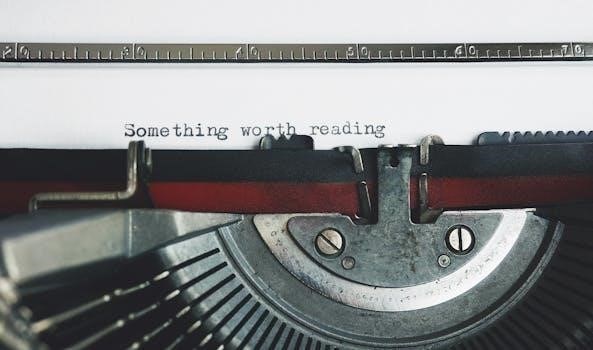
Hobart Tigwave 250 AC/DC: Overview
The Hobart Tigwave 250 AC/DC is a versatile single-phase power source TIG welding system, offering adjustable square wave control. It features trigger hold, pre/post-flow, and crater fill functions. This unit is designed for both AC and DC welding, providing optimal performance through closed-loop circuitry.
The Hobart Tigwave 250 AC/DC is a robust and versatile TIG welding machine, designed to cater to a wide range of welding needs. This model, often found in both industrial and hobbyist settings, is known for its reliable performance in both AC and DC welding modes. Many users have noted its durability, with some machines operating effectively for over two decades. The unit’s adaptability is further enhanced by its inclusion of adjustable square wave control, pre and post-flow settings, and a trigger hold feature, making it suitable for various welding applications. It is a single-phase power source that incorporates closed-loop circuitry to help ensure consistent welding performance. While some older units may have faded control panel markings, user manuals downloaded from the internet can help users navigate its functions. Despite its age, the Hobart Tigwave 250 AC/DC remains a sought-after machine for its strong welding capabilities and dependable operation.
Key Features and Specifications
The Hobart Tigwave 250 AC/DC is equipped with several key features that enhance its welding performance and versatility. This machine offers both AC and DC welding capabilities, allowing users to weld a variety of materials, including aluminum and steel. It incorporates an adjustable square wave control, which is crucial for achieving precise and clean welds, especially when working with aluminum. The Tigwave 250 also features pre and post-flow controls, which help to protect the weld area from contamination and ensure high-quality results. A trigger hold function allows for more comfortable extended welds. The unit is designed with closed-loop circuitry, which contributes to stable and consistent arc characteristics. The power on/off switch is manually operated, and the welding mode can be easily selected between AC and DC. The machine also has settings for High Frequency (HF) start and continuous operation. Although some older models may have faded labels on the control panel, the core functionality of the machine remains reliable.
Hobart Tigwave 250 AC/DC: Operation and Controls
The Hobart Tigwave 250 AC/DC features a control panel with numerous settings for precise welding. Users can select between AC and DC modes, adjust amperage, and utilize HF start or continuous options for optimal control.
Understanding the Control Panel
The Hobart Tigwave 250 AC/DC’s control panel is a central hub for managing welding parameters, though users of older models often encounter faded labels, making identification difficult. This panel includes a power ON/OFF switch and a welding mode selector for AC or DCEN (straight polarity). The panel provides settings for amperage control, often managed via a foot pedal. Given the numerous control options, users must carefully adjust settings to prevent issues like tungsten melting. The high frequency start function is also managed here, with options for continuous or start only. Some users have reported stiff selector switches, which can indicate dried-up grease within the mechanism. It’s crucial to understand each control to ensure proper welding performance, and consulting the manual is recommended to identify each control if labels are faded. The control panel, while complex, is essential for tailoring the welding process to specific materials and project requirements, allowing for versatile welding capabilities.
Welding Modes⁚ AC and DC
The Hobart Tigwave 250 AC/DC offers both Alternating Current (AC) and Direct Current (DC) welding modes, catering to a wide range of materials. DC mode, particularly with high frequency start, is used for welding steel. In DC mode, the machine should provide a strong and stable arc, and the high-frequency start should function correctly. Conversely, AC mode is essential for welding aluminum, which requires the alternating current to clean the oxide layer on the material’s surface. Problems have been reported when switching to AC mode, with users experiencing a very low power output, sometimes only around 10 amps. This indicates a possible issue within the AC circuitry. Some users have found that while DC mode functions flawlessly, the AC mode struggles to provide sufficient power, highlighting the need to carefully examine the AC/DC selector switch and its related connections. Understanding the appropriate mode for each material is critical for successful welding.
HF Start and Continuous Settings
The Hobart Tigwave 250 AC/DC features a High-Frequency (HF) start system, which is crucial for initiating the welding arc without physically touching the tungsten electrode to the workpiece. This system is particularly important in TIG welding, ensuring a clean and precise start. The machine provides both HF start and continuous settings. For welding steel, the HF start setting should be used, which initiates the arc and stops once established. The continuous HF setting is intended for specific applications and may lead to issues, such as melting the tungsten tip if used incorrectly. However, several users have reported issues with the HF start, especially in AC mode, where the arc either fails to start or exhibits erratic behavior. It is important to check that the spark gap is clean and set correctly, typically around .010 inches, for proper HF functionality. Cleaning and adjusting the points can be crucial for the HF system’s correct operation.
Hobart Tigwave 250 AC/DC: Troubleshooting and Maintenance
Troubleshooting the Hobart Tigwave 250 AC/DC often involves addressing issues like no power in AC mode or a malfunctioning HF start. Regular maintenance, including cleaning and adjustments, can help ensure optimal performance and longevity of the welder.
Common Issues⁚ No Power in AC Mode
One frequent problem reported with the Hobart Tigwave 250 AC/DC is the absence of power when operating in AC mode, particularly when attempting to weld aluminum. Users often describe experiencing a situation where the high-frequency (HF) start activates, but the welding arc is either very weak, producing only around 10 amps, or non-existent. This problem often occurs despite the machine working correctly in DC mode, leading to confusion and ruling out common issues such as the foot pedal. A primary suspect in such cases is the AC/DC selector switch, which may have loose lugs or corroded contacts, particularly after years of service. Additionally, dried-up grease in the switch mechanism can lead to stiffness and potential malfunctions. Components like diodes or SCRs could also be implicated, which can be challenging to diagnose and replace without proper schematics and technical expertise. It’s also important to check the remote panel control select switch to ensure all contacts are making proper connection, as a stuck control circuit could result in low output.
Troubleshooting the High Frequency Start
Issues with the high-frequency (HF) start on the Hobart Tigwave 250 AC/DC are another common concern among users. A frequent symptom is the HF attempting to initiate the arc but failing to do so consistently without scratching the tungsten against the workpiece. This can manifest even when the machine is set to the HF continuous setting. Users should begin troubleshooting by verifying that the spark gap is appropriately set, usually around 0.010 inches and perfectly clean. It’s crucial to ensure that the machine is set to HF start mode, not continuous when welding steel, as continuous HF is less robust in this model compared to other machines. If cleaning and adjusting the spark gap does not resolve the issue, the problem may lie within the HF circuitry itself. This could involve components like the spark gap points, which may require cleaning or replacement. If the problem is not related to the spark gap, then it is necessary to look at other causes.
Maintenance⁚ Cleaning and Adjustments
Regular maintenance is essential for ensuring the Hobart Tigwave 250 AC/DC operates at peak performance and extends its lifespan. One of the crucial maintenance tasks is cleaning the machine. Users should periodically clean the exterior of the welder to remove dust and debris, which can accumulate over time. Particular attention should be paid to the internal components, and the spark gap as well; The spark gap should be kept clean and adjusted to the manufacturer’s specifications, usually around 0.010 inches. The selector switch should also be maintained; The switch can become stiff due to dried grease; therefore, disassembly, cleaning, and re-greasing may be necessary. It is also crucial to check and maintain the remote panel control select switch, making sure all contacts are making proper connections. Proper maintenance reduces the risk of common issues, and ensures a consistent welding experience.
Hobart Tigwave 250 AC/DC: Manuals and Resources
Finding the correct user manual is crucial for proper operation and maintenance. Hobart support can provide manuals via email, while parts may need to be sourced from ESAB. Schematics are also available.
Finding and Downloading User Manuals
Locating the user manual for the Hobart Tigwave 250 AC/DC is essential for understanding its operation, troubleshooting issues, and performing maintenance. The official Hobart website is the primary resource for obtaining these documents. While direct downloads might not always be readily available, contacting Hobart support is a reliable method. They often provide manuals via email upon request, ensuring you have access to the necessary documentation. It’s worth noting that while Hobart support can provide manuals, they might not assist with parts or technical issues beyond what is contained within the manual. For specific parts, you would typically need to contact ESAB. Many online welding forums and communities might also contain links or shared copies of the manual. However, always verify the source of these documents to ensure their authenticity and accuracy. Having a digital copy of the manual allows for easy access and referencing during setup, operation, and troubleshooting of the welder. Remember to search for the exact model number, SP7114-001, to ensure you obtain the correct manual for your specific unit. Utilizing the manual will help extend the life and performance of your equipment.
Schematics and Wiring Diagrams
Accessing the schematics and wiring diagrams for the Hobart Tigwave 250 AC/DC is crucial for in-depth troubleshooting and repairs, especially if you are comfortable with electronics. These documents provide a detailed layout of the internal components and their connections. Obtaining them often involves contacting Hobart support through their official website, as they are not always readily available as direct downloads. Requesting these diagrams can be done alongside a request for the user manual. Be prepared to provide your welder’s specific model number, SP7114-001, when making your request. These diagrams are useful when dealing with issues such as power problems in AC mode or when trying to understand how the high-frequency start system operates. Online welding forums and communities might have users who have shared these diagrams, but verifying their accuracy is essential. Utilizing these diagrams alongside the user manual will help in identifying faulty components such as diodes or SCRs. The schematics are critical if attempting to repair or modify any part of the welder and should be used by individuals with an understanding of electrical systems. These diagrams will help you maintain the welder for a longer time.